Industrial fans, essential for powering wind-driven machinery and tools, consist mainly of impellers, casings, inlet diffusers, guide vanes, and motors. Advancements in Industry 4.0 technology are driving these fans towards intelligent, efficient, and energy-saving features. They find extensive applications in diverse fields like refrigeration, mining, metallurgy, equipment production, rail transportation, and marine engineering.
Integral to industrial production, industrial fans demand careful consideration of operating conditions and purposes, setting high standards for design, manufacturing, and testing. The MCU chip, functioning as the control component, must deliver stable, efficient performance, meeting strict industrial reliability standards and addressing complex environmental temperature requirements.
Geehy's APM32F030x8 MCU series is specifically designed for industrial applications, featuring a 32-bit ARM Cortex-M0+ core. Emphasizing product reliability, stability, and power efficiency, this MCU serves as an optimal control core for industrial fans, enhancing real-time control capabilities. With versatile peripherals, it facilitates signal collection from different fan modules through multiple interfaces, ensuring machine protection and stability in various working environments.
Robust Core for Performance Assurance
The APM32F030x8 MCU runs at 48MHz with 64KB Flash, ensuring dynamic real-time performance. Its broad operating temperature range (-40℃ to +105℃) suits industrial high and low-temperature environments. Robust anti-interference capability and increased tolerance to electromagnetic environments ensure stable system operation in complex conditions.
Rich Resources for Precision Control
The APM32F030x8 industrial fan solution features circuits focused on the MCU's control core, temperature, PWM output, current sampling, and fault protection. With various communication interfaces, it easily connects to screen displays, voice output, and start-stop buttons, enhancing user-friendly interaction.
The MCU enables 6 channels of complementary output 16-bit PWM, improving motor control precision. It also supports 12-bit precision ADC sampling for accurate monitoring of current through single/three-resistor sampling methods. This ensures precise sampling for both sensed and sensorless FOC loop control.
Motor Drive Principle
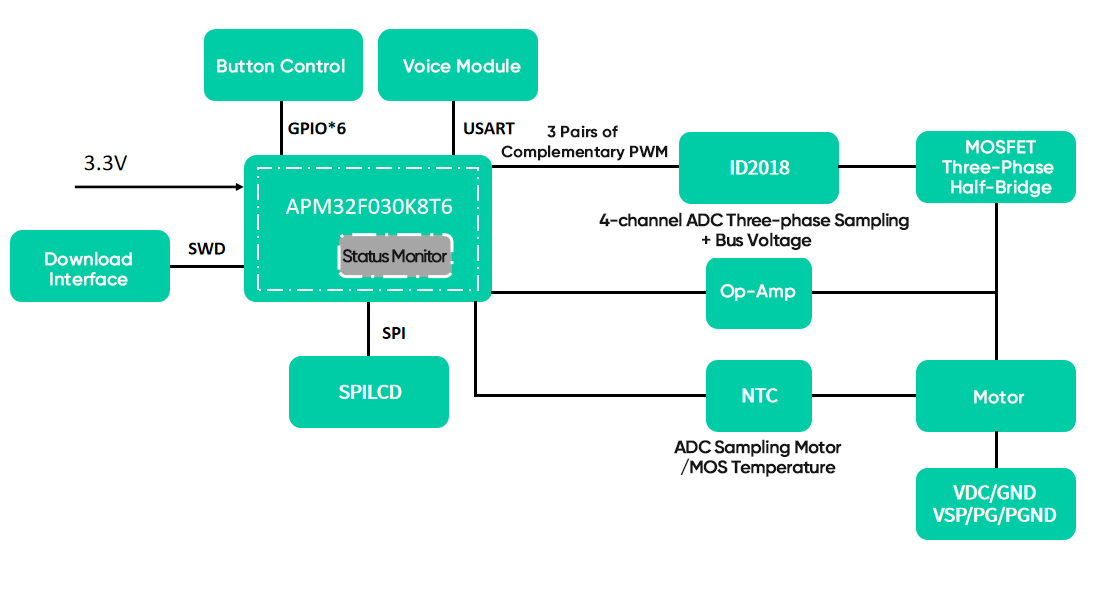
The MCU captures the stator's current signal, sending it to the APM32F030x8 chip through the current sampling circuit. Utilizing resistor sampling, the chip identifies the stator winding's counter-electromotive force, estimates the rotor's current position, and performs initial position detection. Internally, the chip calculates and adjusts to obtain the required motor drive current and voltage. The refined signal is PWM output to the inverter bridge, achieving precise motor control.