Geehy Semiconductor has long been working in the mid-to-high-end industrial control market. In this issue, the absolute encoder, high-performance servo driver, and VFD solutions are used as examples to introduce the outstanding performance of Geehy's 32-bit APM32 industrial-grade MCUs.
Intelligent Absolute Encoder with Promising Market Potential
Considering application requirements, usage environment, and costs, Geehy provides two absolute encoder solutions:
1. Used in Photoelectric and Magnetoelectric Absolute Encoders
In this solution, APM32F103 industrial grade MCU is mainly used to read single-turn position, monitor voltage, calculate the number of turns and implement encoder protocol, which needs to be used with an encoder single-turn chip.
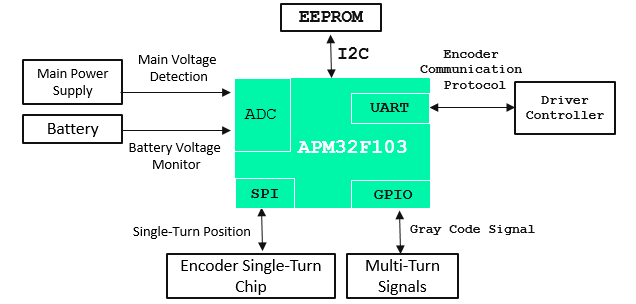
Option 1: MCU doesn’t support position calculation
2. Used in Photoelectric Absolute Encoder
In this solution, the APM32F103 industrial-grade MCU is mainly responsible for collecting the sine and cosine analog signals from the optical and magnetic sensors, monitoring the voltage, calculating the number of turns, and implementing the encoder protocol.
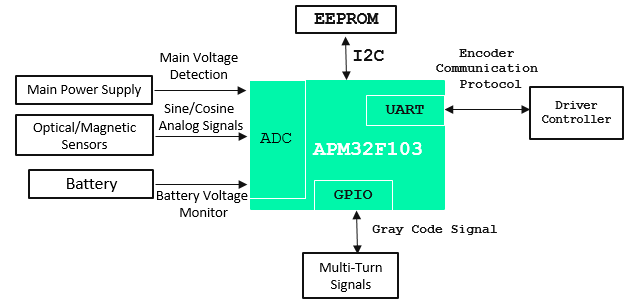
Option 2: MCU supports position calculation
APM32 Absolute Encoder Solution
• Based on the industrial-grade mainstream APM32F103 MCU with Arm Cortex-M3 core
• Operating frequency 96MHz, Flash 16512KB, SRAM 6128KB
• Two 12-bit high-precision ADCs supporting 16 input channels for dynamic real-time sampling
• Two SPI interfaces with a maximum communication rate of 18Mbit/s for efficient encoder data handling
• Three USART interfaces, including USART1 with a maximum communication rate of 4.5Mbit/s, ensure high-speed and reliable encoder communication
• Flash page erase time ≤1.51ms, facilitating efficient encoder register data management
• Low power consumption of 12uA in STOP mode, ensuring prolonged battery life
• Certified IEC 61508 SIL3, meeting rigorous industrial reliability standards
Integrated High-Performance Servo Drive with High Power Density and Low Cost
The servo driver is an important part of modern motion control, which controls the servo motor through position, velocity, and torque to achieve high-precision positioning of the transmission system. It's a high-end product that uses drive technology and is widely used in industrial robots, CNC machine tools, and other automation equipment.
Geehy's high-performance servo driver platform supports a variety of advanced algorithms, including resonance suppression, mechanical parameter identification, adaptive notch filter, fractional-order control, PWM update, etc. With excellent performance, the current loop bandwidth is up to 4KHz and the speed loop bandwidth is greater than 800Hz. The built-in 100M EtherCAT supports a high synchronization cycle and low jitter clock. The APM32F407+FPGA+IPM architecture has powerful secondary development and flexible expansion space, which makes it easy to package, develop collaboratively and maintain.
APM32 High-Performance Servo Driver Solution
• Adopt APM32F407 industrial-grade high-performance MCU
• Based on Arm® Cortex ® -M4 core
• Operating frequency: 168MHz; Flash 1MB, SRAM 192+4KB, SDRAM 2MB (optional)
• Use CAN bus to realize motor control command transmission
• The used software makes it easy to adjust host computer parameters
• Built-in EMMC facilitates efficient communication with peripheral FPGA
• Rich peripherals support integrated motor/driver/reducer with high power density
• Use a magnetic encoder to realize position feedback, more seismic, corrosion resistance, high reliability, and simpler structure
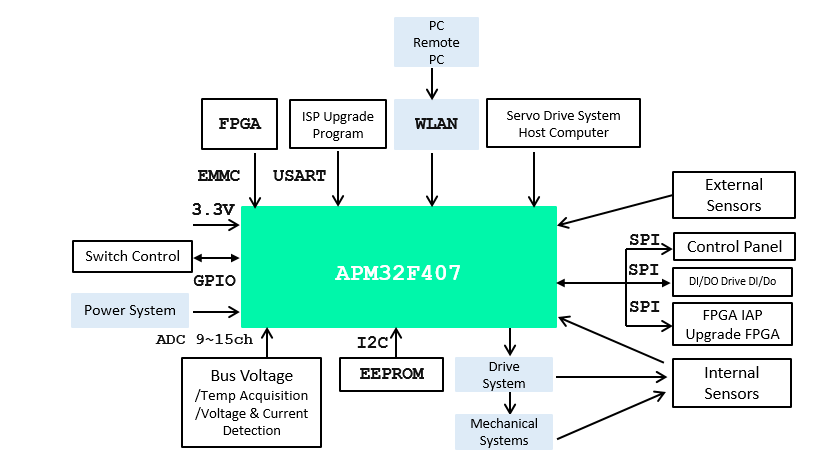
APM32F407 is Used as A Master MCU in the Servo Drive Platform
• As an interface for human-machine interaction, a switch can control the motor's start and stop.
• Calculate to generate position references for servo drives, such as low/high speed, forward/reverse sine wave, and ramp position
• Act as EtherCAT master, detects the number of slaves, generate data frames, and transmit them through the network port
• Act as serial communication, part of the process data is sent during debugging, which is convenient for data analysis and auxiliary debugging
Variable-Frequency Drive(VFD) Helps Motor Reduce Consumption and Save Energy
The VFD, utilizing advanced frequency conversion and microelectronics, is a crucial power control device for AC motors. It optimizes energy usage by adjusting the motor's frequency. Widely used in fans, pumps, central air conditioners, and mechanical equipment like transmission and machine tools, VFDs enhance process efficiency, product quality, and equipment lifespan by enabling speed control and energy reduction.
Geehy's VFD solution, featuring APM32F4 MCUs, gives precise power to motors, saving energy and controlling speed, meeting industrial automation needs.
Single-chip Solution: APM32F407
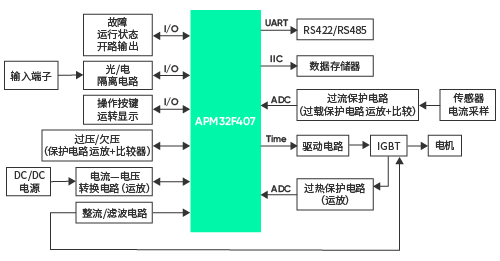
Dual-chip Solution: APM32F405+APM32F030
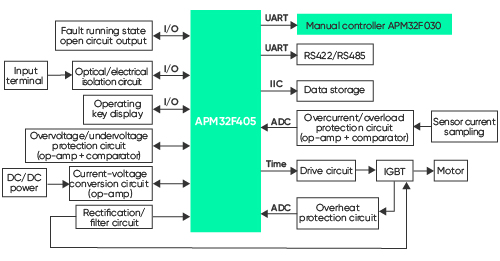
Based on the APM32F4 MCU series (Cortex-M4)
• Operating frequency 168MHz, with efficient FPU computing capability
• External memory expansion
• Vector control, V/F control, parameter self-identification
• Complementary PWM output with dead zone and brake protection
• High-speed GPIO processing and three 12-bit high-precision ADCs for enhanced response speed and torque control
• Compatibility with multi-mode expansion cards or encoder interfaces
In the evolving landscape of industrial intelligence, Geehy remains committed to delivering efficient, stable, and secure industrial equipment systems. With a steadfast focus on market and technological advancements, we collaborate closely with partners to offer comprehensive industrial application solutions.