Encoders are primarily categorized based on their measurement principles into optical and magnetic types. Magnetic encoders offer several advantages over optical encoders, including:
· Dust-proof, oil-resistant, and vibration-resistant
· Simplified debugging and installation
· Smaller size with equivalent precision
· Adaptability to harsh environments
According to Future Market Insights, the global encoder market is projected to grow at a compound annual growth rate (CAGR) of 7.6%, increasing from $2.3 billion in 2023 to $4.8 billion by 2033. Industrial magnetic encoders represent a key growth area with significant potential.
Geehy Magnetic Absolute Encoder Solution Overview
The MCU is the core component in encoder design, directly impacting system performance. Geehy's APM32F103xB-based magnetic absolute encoder solution supports applications requiring 16–21-bit angular resolution. It is ideal for industrial control and consumer electronics, providing precise positional data for system control.
Solution Features
· High Precision: Provides 17-bit single-turn resolution with angular accuracy < ±0.5° before calibration, and < ±0.07° after calibration.
· Low Power Consumption: Supports 16-bit multi-turn information, with static average current < 20μA during battery operation, and a 1,100 mAh battery lifespan exceeding 5 years.
· High Communication Speed: RS485 communication rate reaches 4 Mbit/s, reducing communication time and enhancing real-time data transmission.
· Compact Design: Achieves a PCB diameter as small as 35 mm, suitable for servo motors with a 40 mm flange.
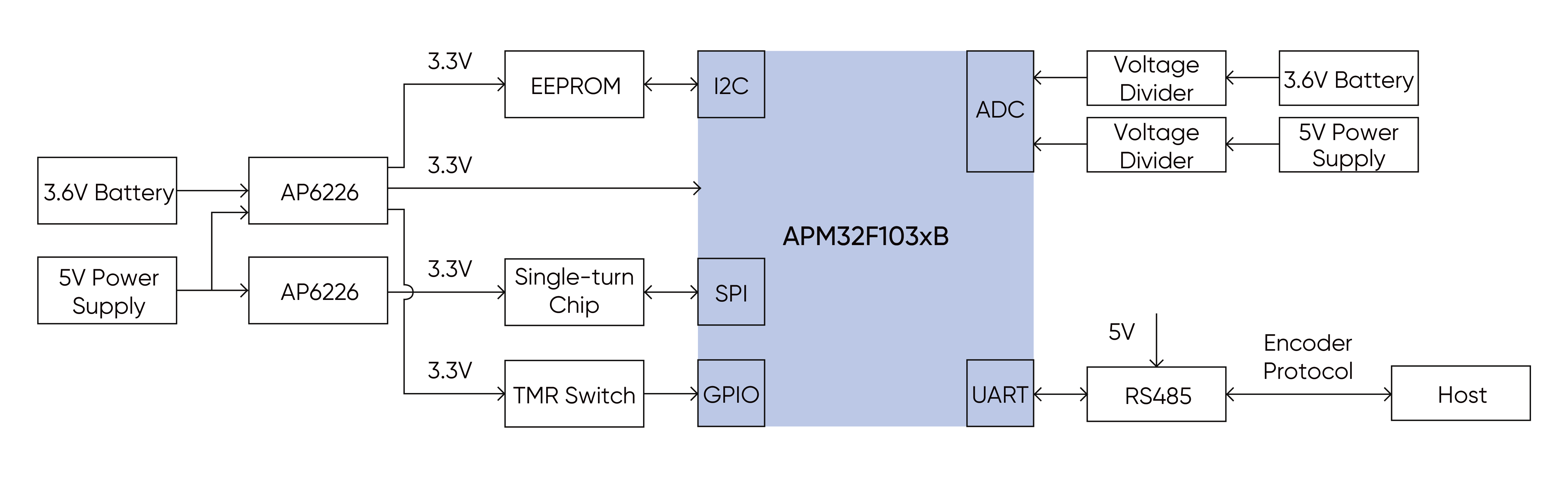
Solution Block Diagram
PCB Resources and Basic Functions
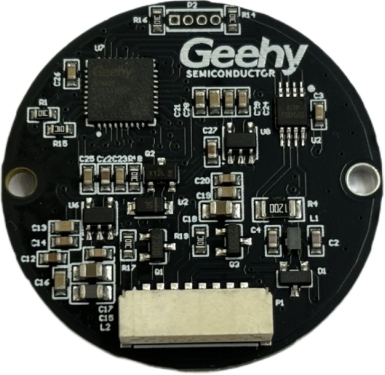
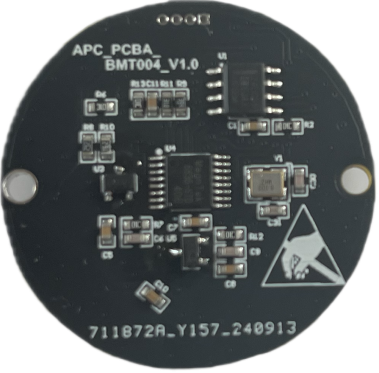
Physical PCB Diagram
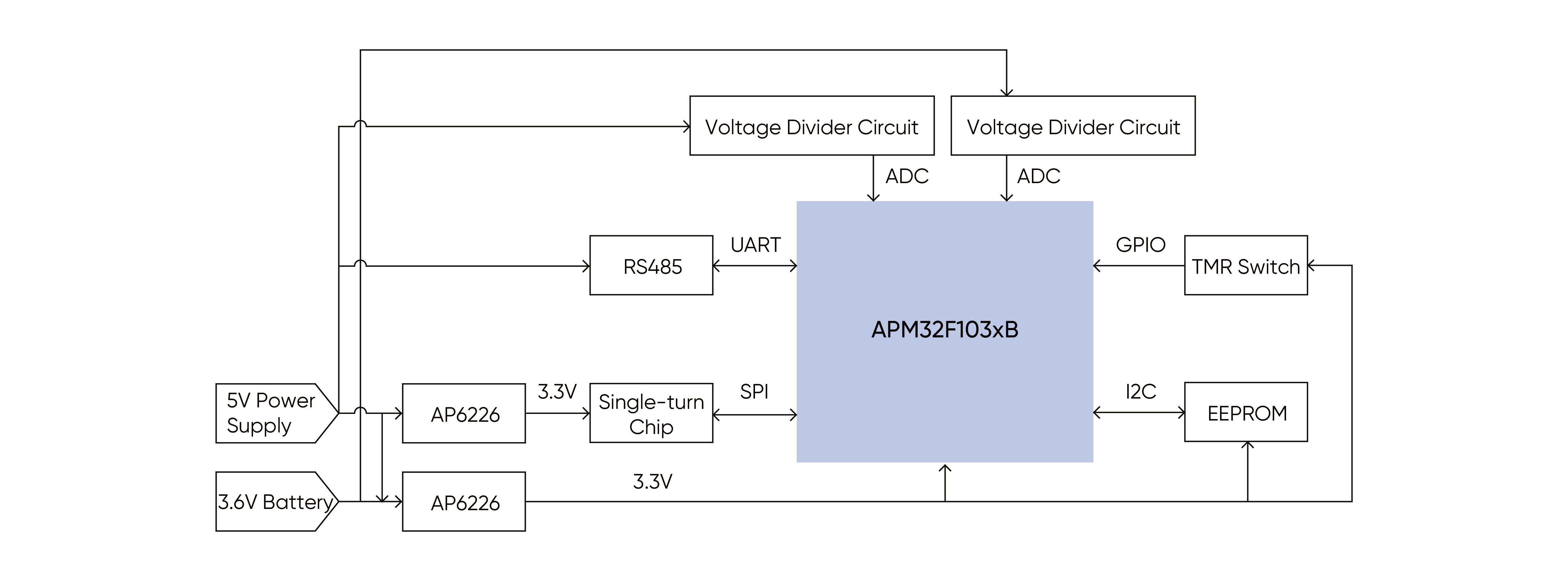
PCB Hardware System Block Diagram
Basic Functions
· The APM32F103xB reads single-turn positional and alarm data via SPI.
· GPIO pins are utilized to monitor two timer switch states for multi-turn information calculation.
· I2C is used for data storage/retrieval with the host device.
· USART is implemented for achieving encoder protocols and communicating with the host device.
· ADC is engaged to sample battery and main power voltages, enabling voltage monitoring and fault alerts.
Note: Due to the erase and programming time for a 1KB page in the APM32F103xB FLASH being under 2 ms, FLASH can also emulate EEPROM for storing and reading data.
Performance Advantages of the Industrial-Grade Mainstream APM32F103xB MCU
· Low Power Mode: Stop mode current as low as 12μA; Standby mode current as low as 5μA.
· Compact Package: Features a 6×6 mm QFN36 package, ideal for low-power, compact designs.
· High-Speed UART: Communication speed of up to 4.5 Mbit/s, meeting encoder protocol requirements (2.5 Mbit/s or 4 Mbit/s).
· High-Speed SPI: Maximum communication speed of 18 Mbit/s, enabling fast read/write operations for single-turn encoder chip data.
· High Reliability: Certified for IEC60730 CLASS B and IEC61508 SIL3, with an operating temperature range of −40°C to 105°C.
· High Operating Frequency: Arm® Cortex®-M3 core with a clock speed of up to 96 MHz.
Complete Software and Hardware Ecosystem: Provides comprehensive software and hardware support, including demo boards for the entire development process of magnetic absolute encoders.
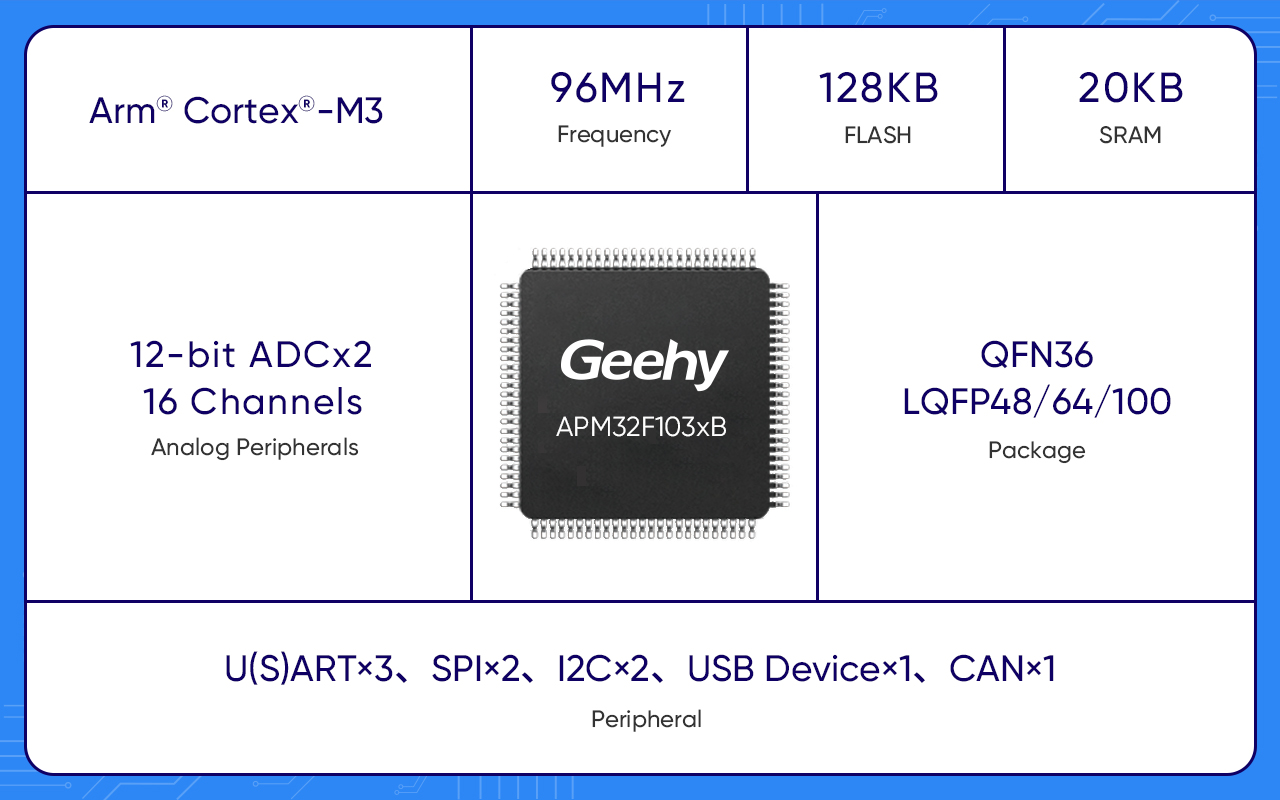
Targeting the encoder application market, Geehy leverages its high-performance APM32 industrial-grade MCU product line, experienced design teams, and responsive technical support to meet the diverse needs of industrial control and consumer electronics applications. Geehy has established strong collaborations with multiple end manufacturers and continues to innovate in product development to drive the encoder industry toward higher precision, intelligence, and cost efficiency.

Geehy's APM32F103xB encoder solution includes detailed specifications, reference designs, example code, schematics, and PCB design files. For further inquiries, please contact us!