The servo controller is one of the important components in the modern demand for motion control with its highest possible level of performance for precise control of position, velocity, and torque. It has been used in the industrial field of printing equipment, laser processing equipment, textile equipment, robotic arms and other products, and also creates the possibility for the future of adaptive control, artificial intelligence, fuzzy control, variable structure control, neuronal networks, and other fields of the next generation of results.
Geehy's servo controller solution adopts APM32F407 series MCU based on ArmCortex-M4 core. With the high main frequency and multiple peripherals, this series meets the performance and flexibility requirements of the main control chip for the servo controller and can cooperate with FPGA to realize the functional applications of information acquisition, communication, and control in the servo system.
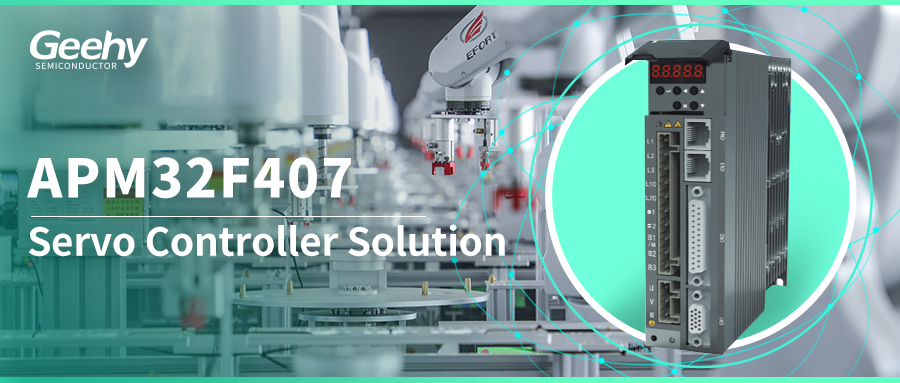
High-Performance Chip Safeguards Core System
Comes with a frequency of up to 168MHz, the APM32F407 series MCU can be properly overclocked at room temperature to meet high real-time applications such as US-level current loop control of servo control systems. It supports single-precision FPU and sets enhanced DSP processing instructions, has 1MB FLASH and 192KB SDRAM,
supporting external memory expansion to meet system design requirements and guarantee its real-time responsiveness. The operating temperature covers -40℃~+105℃ with strong anti-interference ability and higher tolerance to the electromagnetic environment, which can adapt to a complex industrial working environment.
Rich Peripherals for Precise Control
Rich application peripherals enable the chip to meet the connection and application scenarios of rich peripheral devices of a servo control system, which allows the integrated design of the motor, driver, and reducer to fully optimize the system. Built-in EMMC interface and 100ns wait timing facilitate efficient communication with peripheral FPGA. High ADC sampling accuracy can accurately monitor the bus current to achieve effective closed-loop control. The CAN bus enables motor control command transmission with both stability and efficiency.
Combining Adaptability & Security
The APM32F407 series MCU can be configured with BOOT [1:0] pins to boot from System Memory, Flash and SRAM, and the memory selected as the boot area is determined by the boot mode, which is convenient for users to develop and test. The built-in true random number generator supports AES, DES, and TDES encryption standards, while adding SM3 and SM4 algorithms to adapt to the domestic development environment and effectively ensure the security of users’ product information.
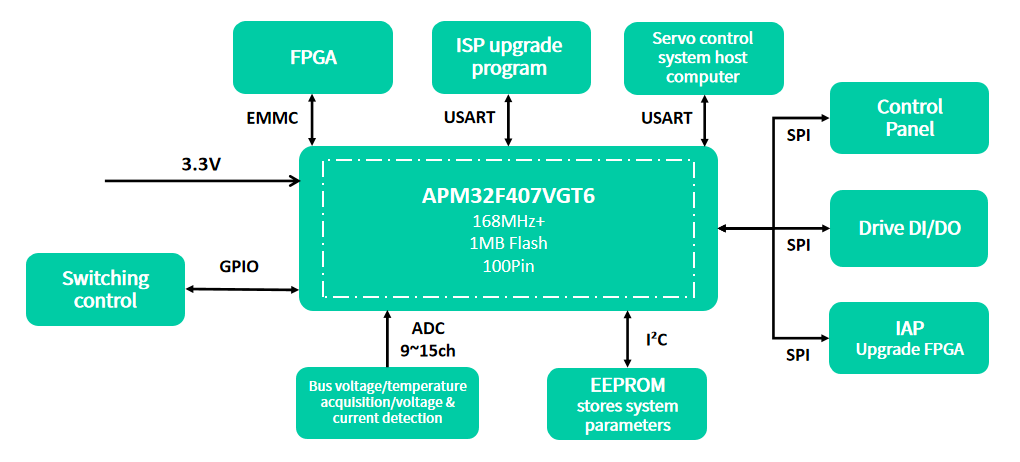